What We Do?
Grace Supply Chain Solutions offer a diverse range of Job works & Fabrication work flowing thru various process such as CNC precisions turning, VMC milling, Centerless, Cylindrical, ID Grinding & Surface Grinding, Honing, Polishing, Burnishing, Anodizing, Electro Plating & Powder Coating.
We also have specialized sources for Wire Cutting, EDM, Laser Cutting, Water JET Cutting & Plasma cutting for profiled jobs.
We also have a greater Heat Treatment Sources for various components like SQF Furnace, Salt Bath Heat Treatment Process, Case Hardening, Carbo Nitriding, Vacuum Hardening for D2, M2 & HCHCR materials.
We have specialized HT Sources for cryogenic heat treatment process.
.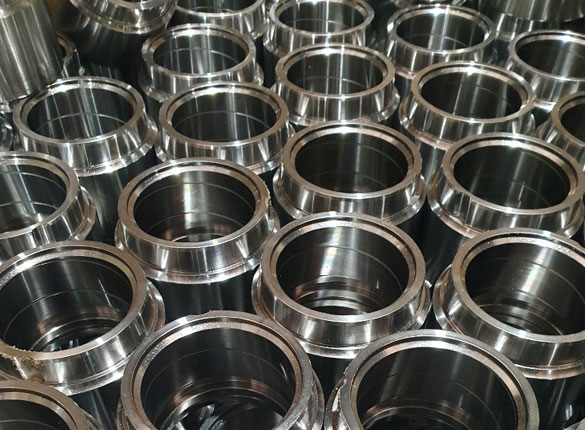

Why Choose Us?
Grace Supply Chain Solutions provides a one point service for your entire manufacturing process i.e. Starting from Raw Material to Finish component all the process will be done by us under qualified processing methods. In simple words, Place your order get your materials.
For Cost effective, Qualified & Timely delivery of machined components.
Our experience in this field helps to study & stabiles the process required for your component by which the cost of component can be reduced & 0 PPM can be achieved.
Special process required, can be carried out with the suggestion on experts in our team to make your components as per requirement .
Highly precision component tolerance specified in microns can be machined under competitive price.
.Quality Policy
Grace Supply Chain Solutions strives to be an increasingly customer oriented organisation aiming for the pinnacle of customer satisfaction, with focus on productivity, defect free products and timely delivery of precision engineered components in the international market and precision engineered components and production components including casting & fabrication in the domestic market. This will be realised by:
.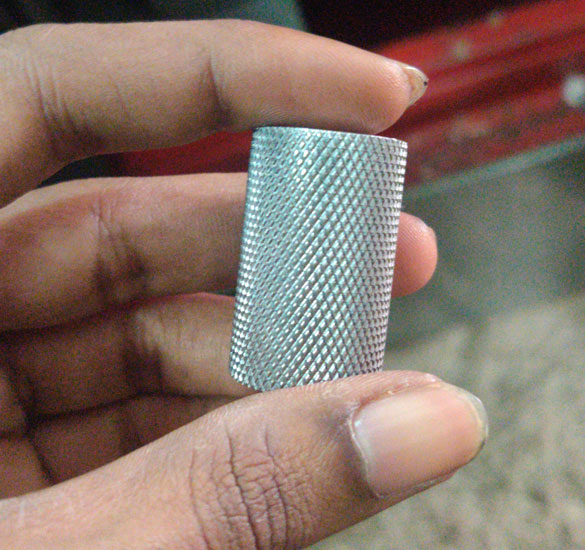